SAP Dairy Management by msgSAP
Accelerate decision-making with real-time insight.
Vendor
SAP
Company Website
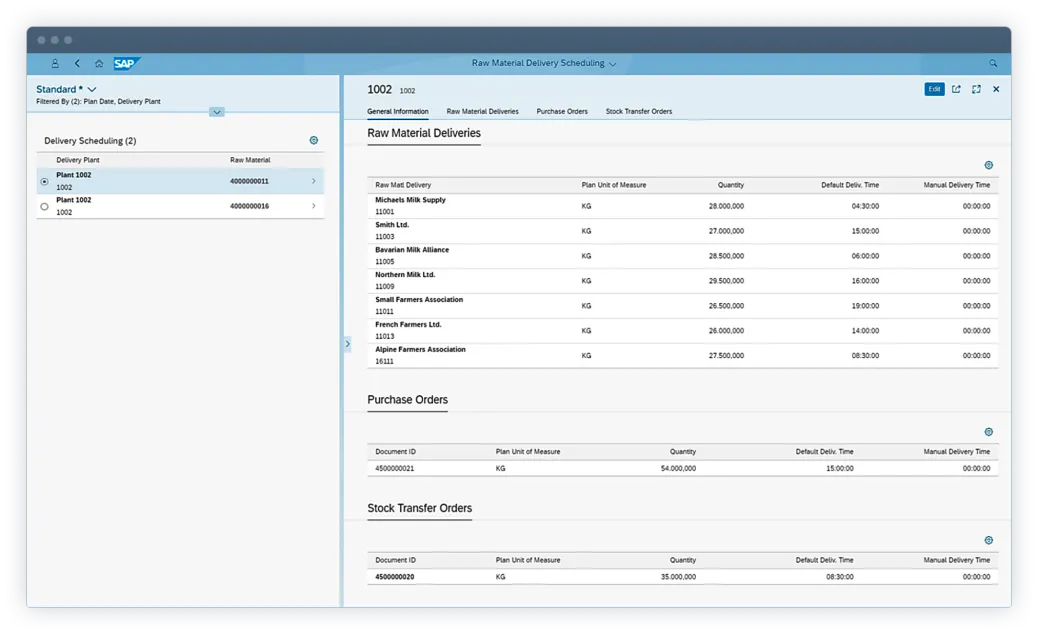
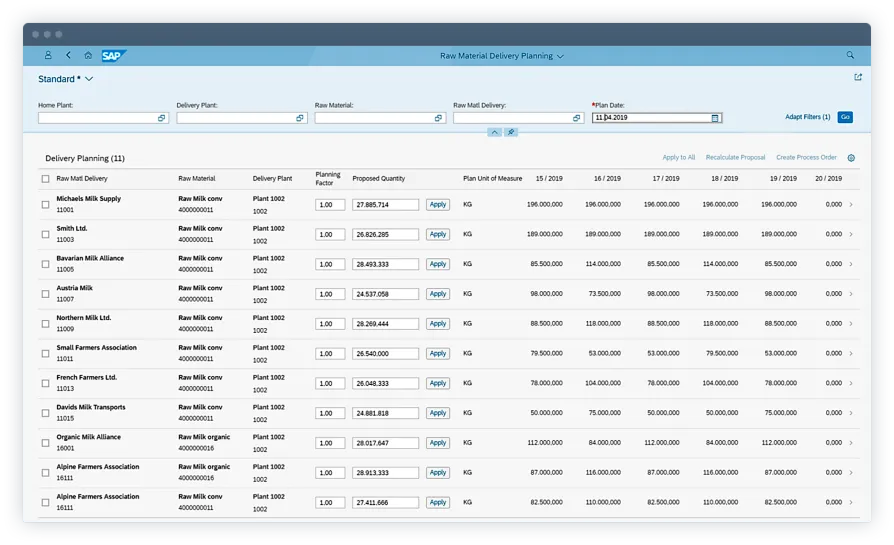
Streamline…stribution.pdf
Product details
Manage the production of dairy products with balance and control
Streamline dairy management from production and processing to distribution
Cover the full scale of your milk production process – from raw milk reception to processing the finished product. With the SAP Dairy Management application by msg, you can take advantage of innovative planning and controlling instruments that are specific to the dairy industry.
- On-premise deployment
- Connectivity between all business users
- Comparison of planned, actual, and target data
- Control of production yield, gain, and loss
Key benefits
Accelerate decision-making with real-time insight
Improve forecast accuracy and on-time delivery based on appropriate allocation of raw milk components to production sites.
Increase end-to-end process visibility
Gain full transparency by combining planning, execution, gain and loss, and inventory data, while delivering dairy-specific reporting.
Reduce production cost and loss
Increase raw material yield by maximizing production efficiency and analyzing raw material and component consumption.
Key features
Efficient raw material and production planning
- Make production and raw material planning more flexible to increase efficiency and prevent loss
- Improve raw material and plant utilization by balancing raw material income and demand
- Support cross-plant planning of raw material deliveries
Dairy and cheese production
- Display key resource figures by the day, such as adjusting machine times and process quantities
- Deliver a milk balancing sheet and comparison of target and actual production at each stage
- Access an overview of raw material losses across the entire company
Dairy activity-based costing
- Adopt planning tools for production, activity, and quantity management
- Plan activity-based cost accounting
- Analyze costing of objects during the planning stage
Find more products by industry
Other ServicesHospitalityWater & Waste ManagementManufacturingMining & QuarryingEducationInternational OrganizationsUtilitiesFinance & InsuranceReal EstateAgriculture & FishingTrade & RepairTransport & StorageHealth & Social WorkAdmin & Support ServicesHousehold ActivitiesProfessional ServicesPublic AdministrationConstructionInformation & CommunicationArts & RecreationView all