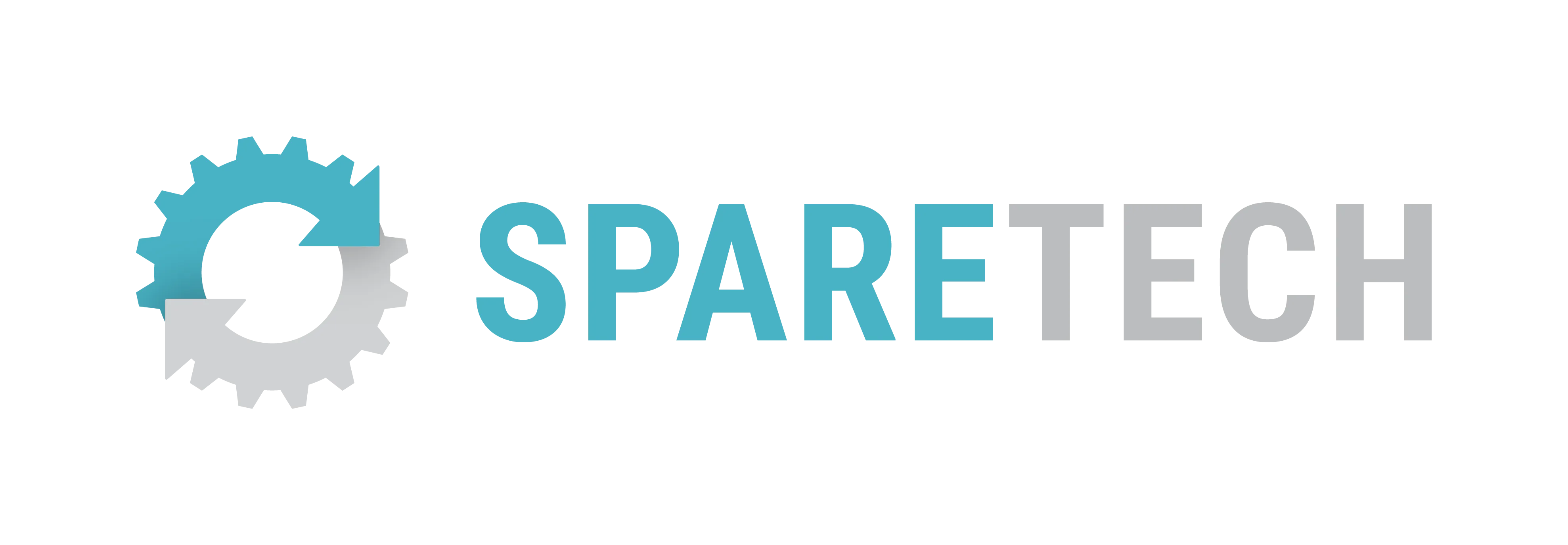
Digital workflow for creating clean, duplicate-free spare parts material records, synced with ERP systems using original manufacturer data.
Vendor
SPARETECH
Company Website
SPARETECH’s Material Creation Workflow is a SaaS solution that streamlines the creation of industrial spare parts material records. It ensures data quality by preventing duplicates, integrates original manufacturer data, and synchronizes seamlessly with ERP systems for error-free spare parts management.
Key Features
Live Duplicate Check Prevents duplicate material entries during creation.
- Real-time matching algorithms check for duplicates in your material master.
- Cross-plant duplicate detection optimizes inventory across multiple locations.
Original Manufacturer Data Integration Ensures accuracy and completeness of material records.
- Transfers 100% correct and complete product data directly into ERP systems.
- Uses a global database of leading manufacturers’ spare parts.
Configurable Request Forms & Approval Processes Customizable workflows for compliance and accuracy.
- Material request forms tailored to organizational needs.
- Approval processes to ensure error-free ERP synchronization.
ERP Synchronization Automates and simplifies data transfer to ERP systems.
- Direct API integration for seamless data exchange.
- Reduces manual entry and associated errors.
Benefits
Improved Data Quality Maintains a clean, reliable material master.
- Eliminates duplicate entries, reducing confusion and excess inventory.
- Ensures all data is accurate and up-to-date.
Operational Efficiency Accelerates material creation and management processes.
- Cuts time spent on manual data entry and duplicate checks.
- Streamlines workflows for faster onboarding of new materials.
Cost Reduction Optimizes spare parts inventory and lowers costs.
- Prevents unnecessary stock by identifying duplicates.
- Reduces inventory holding costs through better data management.