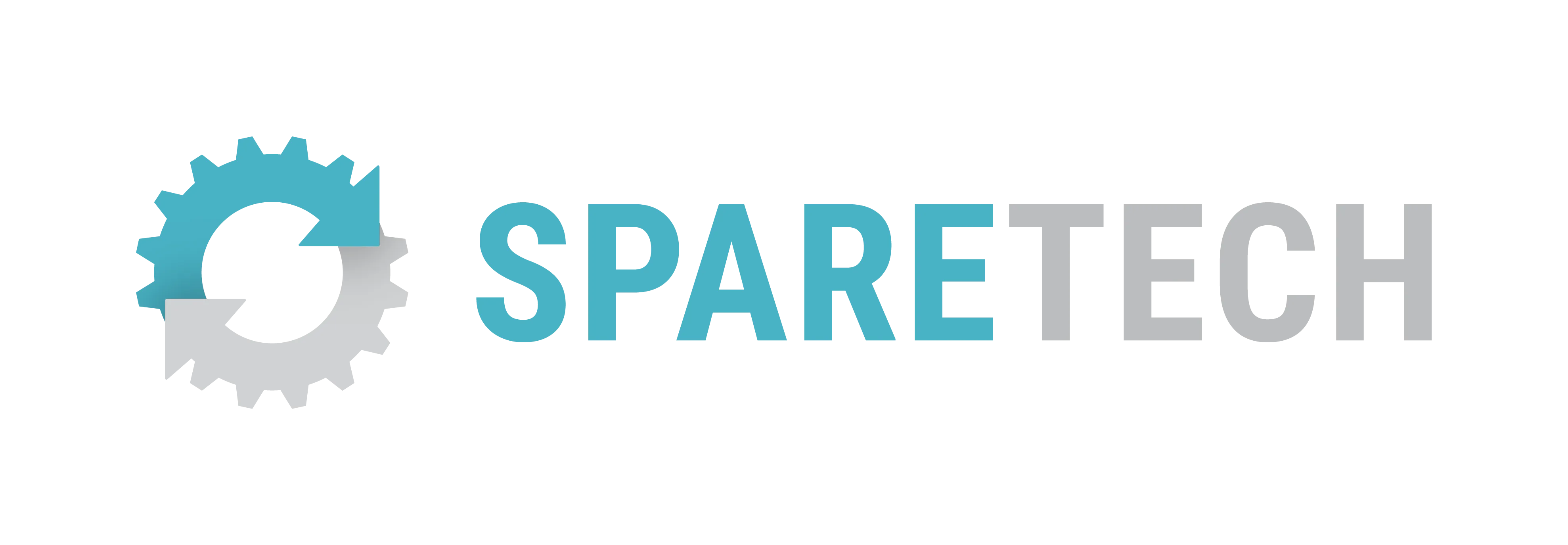
Automated BOM Check identifies duplicates in spare parts lists by matching them with your material master, reducing costs and manual effort.
Vendor
SPARETECH
Company Website
Automated BOM Check by SPARETECH is a software solution designed to analyze and clean spare parts lists (BOMs) by automatically comparing them with your existing material master data. Using intelligent algorithms, it identifies duplicates and missing materials, helping organizations avoid redundant purchases, reduce inventory, and streamline the integration of new materials into ERP systems. The results are presented in an intuitive dashboard, allowing users to visualize and manage their spare parts data efficiently.
Key Features
Duplicate Detection Automatically identifies duplicate items in spare parts lists by comparing with the material master and within the list itself.
- Prevents redundant material creation
- Reduces unnecessary procurement
Intuitive Dashboard Visualizes evaluation results and plant distribution of items for clear project oversight.
- Real-time overview of spare parts data
- Progress tracking for start-up projects
Automated Data Preparation Processes new spare parts lists in various formats (Excel, CSV, etc.) and prepares clean lists for ERP import.
- Quick identification of missing materials
- Streamlined ERP integration
Cost Savings Analysis Finds original part manufacturers to highlight potential procurement savings.
- Highlights lower-cost sourcing options
- Supports average procurement cost reduction
Bulk Processing Capability Handles large datasets efficiently, supporting significant inventory reduction initiatives.
- Manages thousands of material numbers
- Suitable for multi-plant operations
Benefits
Reduced Procurement Costs By eliminating duplicates and sourcing from original manufacturers, organizations save on spare parts purchases.
- Average cost reduction of 13%
- Avoids double purchases
Increased Efficiency Automates manual spare parts list checks, freeing up staff time and accelerating processes.
- Up to 57% faster than manual checks
- Reduces manual workload
Improved Data Quality Ensures only unique, relevant materials are added to the ERP, maintaining a clean and accurate material master.
- Prevents data pollution
- Supports better inventory management
Inventory Optimization Helps reduce excess inventory by identifying and removing duplicate stocks.
- Direct impact on inventory levels
- Enables immediate inventory reductions