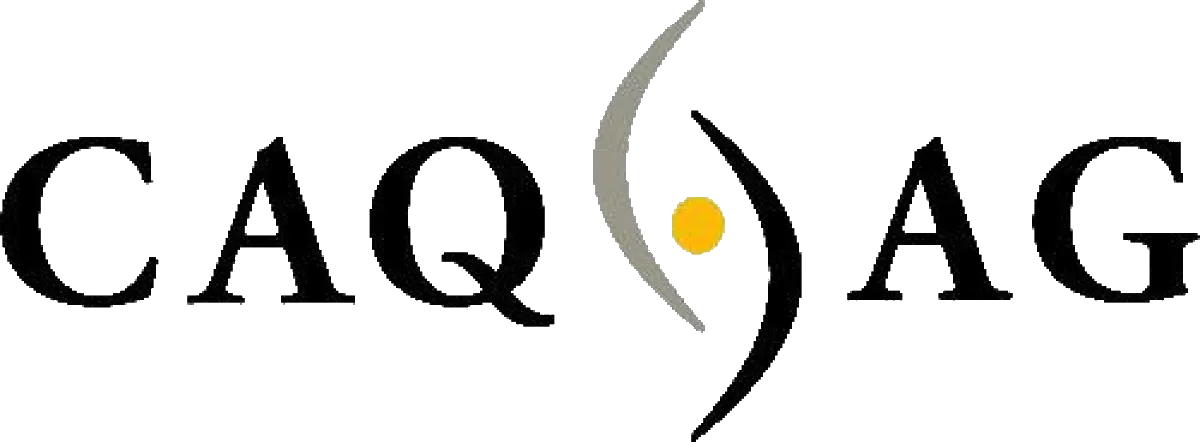
8D Report Software streamlines complaint management by guiding users through eight structured problem-solving steps to improve product quality.
Vendor
CAQ Factory Systems
Company Website
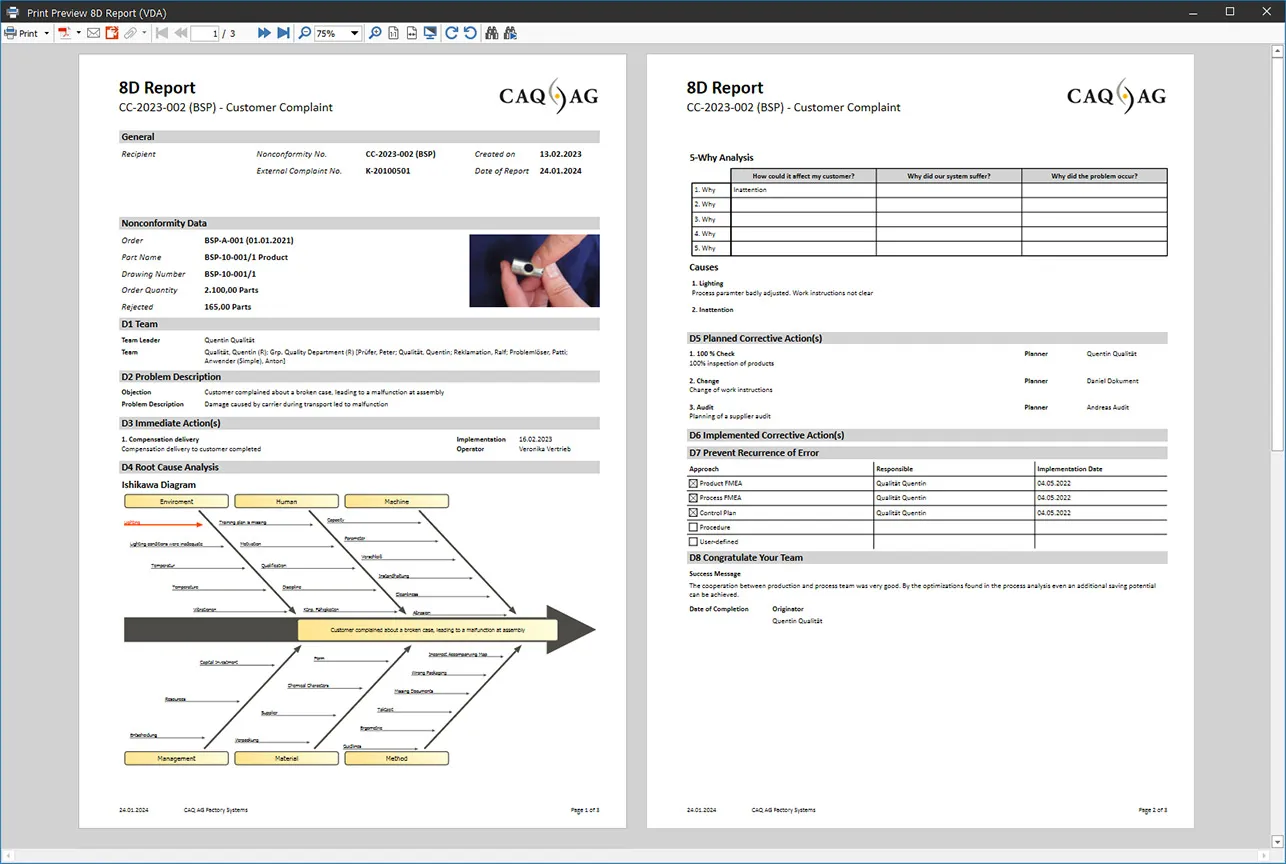
8D Report Software supports the entire 8D problem-solving process in complaint management, facilitating structured documentation and resolution of issues between customers and suppliers. It assists in systematically addressing complaints through eight defined disciplines, from team formation to preventive measures and closure, ensuring no critical step is missed. The software enables effective data acquisition, root cause analysis, corrective action implementation, and preventive strategies to enhance product quality assurance. It often integrates with broader complaint management systems and supports customizable forms and methods beyond the 8D approach.
Key Features
Assistant-based 8D Process Completion Guides users through all eight disciplines of the 8D method to ensure thorough complaint processing.
- D1: Use a Team
- D2: Define and Describe the Problem
- D3: Develop and Implement Interim Containment Actions
- D4: Identify and Verify Root Causes and Escape Points
- D5: Choose and Verify Permanent Corrections
- D6: Implement and Validate Corrective Actions
- D7: Take Preventive Measures
- D8: Congratulate the Team
Complaint Data Management Centralized acquisition and processing of complaint data to streamline customer and supplier interactions.
- Structured documentation of complaints
- Integration with complaint management systems like REM.Net
- Support for customized methods and variance categories
Integration and Automation Seamless integration with other quality management modules and systems to automate workflows and data exchange.
- Links with ERP, CAD, PDM, SCM systems for master and order data
- Automated synchronization with measurement and inspection data
- Supports supplier data integration with secure internet connections
AI Support (in advanced systems) Artificial Intelligence enhances efficiency and accuracy in the 8D process by suggesting preventive measures, deadlines, and responsible persons.
- AI-driven suggestions for preventive actions and FMEA updates
- Automated documentation of lessons learned for future problem solving
- Improves speed and quality of problem resolution
Reporting and Analysis Tools Provides evaluation, analysis, and reporting capabilities to monitor trends and effectiveness of corrective actions.
- Customizable dashboards and checklists
- Root cause analysis tools (e.g., Ishikawa diagrams)
- Real-time progress tracking and notifications
Benefits
Efficient Problem Solving Accelerates the resolution of complaints by automating data capture and guiding structured workflows.
- Reduces manual paperwork
- Ensures no process step is overlooked
- Speeds up corrective action implementation
Improved Collaboration Facilitates teamwork across departments and with external partners such as suppliers and customers.
- Real-time updates and communication
- Shared access to reports and data
- Supports cross-company quality processes
Standardized Quality Assurance Ensures consistent application of the 8D methodology for reliable and repeatable problem resolution.
- Uniform documentation standards
- Compliance with industry quality norms
- Audit-proof record keeping
Enhanced Data Insights Enables better analysis of complaint trends and root causes to prevent recurrence.
- Tracks recurring issues and patterns
- Supports continuous improvement initiatives
- Data-driven decision making
Regulatory Compliance and Traceability Maintains comprehensive documentation for accountability and quality audits.
- Centralized complaint records
- Version control and audit trails
- Supports ISO 9001 and other standards